Edelbrock Foundry: Expanding the Horizons of Aluminum Casting Education
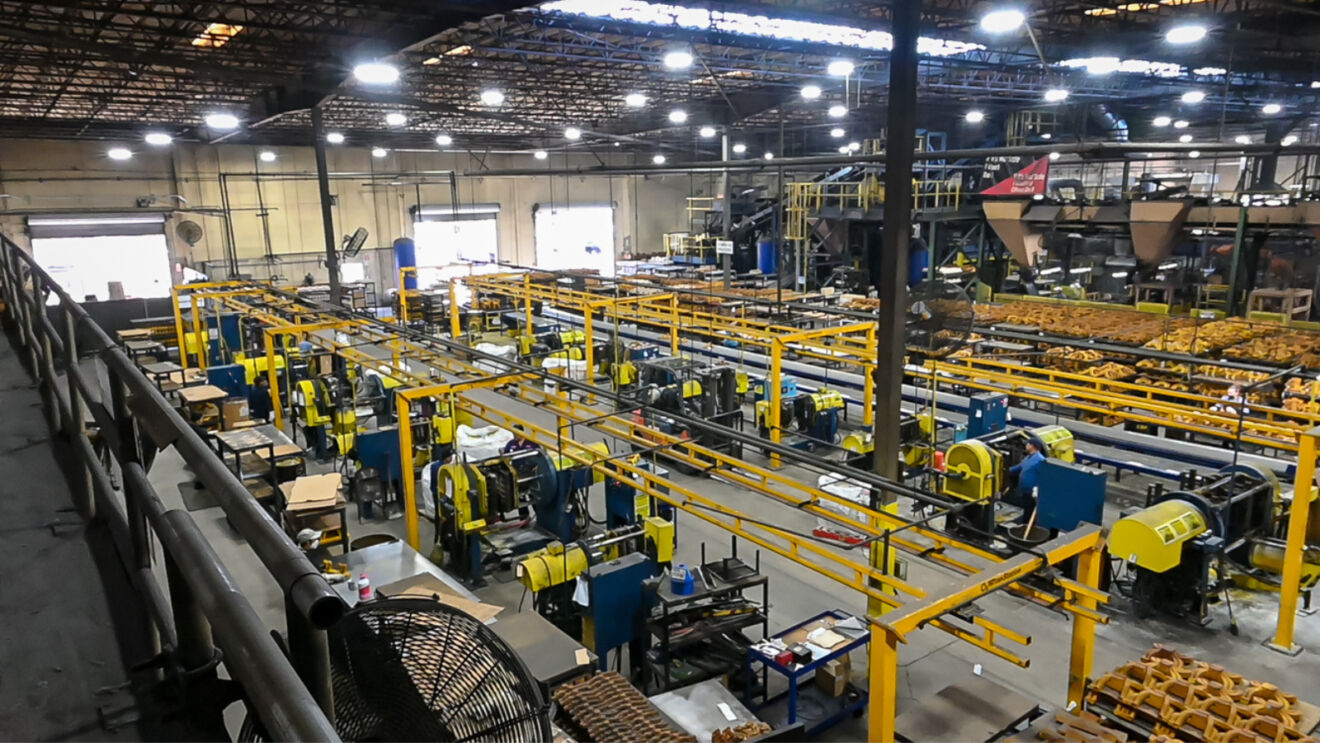
Edelbrock, recognized globally for its aftermarket aluminum parts such as intake manifolds, water pumps, and cylinder heads, is inviting the world to understand the multifaceted capabilities of their Aluminum Foundry in San Jacinto, California.
While Edelbrock’s automotive components are renowned, the foundry’s capabilities extend well beyond this sector. From design engineering, CNC pattern-making to prototyping and finishing, the Edelbrock Foundry provides comprehensive services.
Edelbrock Foundry’s General Manager, Charles Emerson, and Director of OEM and Foundry Sales, Robert Morse, highlight the distinct features of the two 73,000-square-foot facilities. Located strategically in San Jacinto for its arid climate – an essential factor in sand casting – the state-of-the-art aluminum casting facility is a testament to Vic Edelbrock Jr.’s vision of maintaining a ‘Made in America’ ethos.
The foundry specializes in A356 and 808 aluminum and employs three types of casting processes – permanent mold, dry sand, and green sand. With the recent integration of a 3D printer, Edelbrock is positioned to dramatically improve developmental timeframes and costs for short-run castings and prototypes, becoming the only facility with this capability on the West Coast.
“We can go from model to casting in just two to three weeks,” says Emerson. He further adds, “From the other end of the spectrum, we can put it into production.”
The investment in technology also includes a deburring machine designed to optimize the finishing phase. With the ability to rapidly remove rough-casting edges, this machine further emphasizes Edelbrock’s commitment to efficiency.
Beyond the automotive realm, the Edelbrock Foundry’s clientele spans diverse sectors, from agriculture and irrigation to the locomotive industry. The recent collaboration with Lotus, where the Foundry produces superchargers for its 3.5-liter V6 engine, showcases the facility’s versatility.
Emerson and Morse view the Electric Vehicle (EV) market as a new avenue ripe with opportunity. With the rapid evolution of EV technology, the foundry’s adeptness at quick prototyping positions it perfectly to serve this burgeoning sector.
The Edelbrock Foundry seeks clients looking for production ranging from 1,000 to 60,000 units annually. Their strategic shift towards providing turnkey cast-machine parts addresses modern clients’ needs for efficient, consolidated services.
For those interested in leveraging the unparalleled expertise and capabilities of the Edelbrock Foundry, the Edelbrock Foundry website offers an inquiry page for a seamless quote generation process.
Edelbrock continues to uphold its legacy of high-quality American-made aluminum parts. With the expansion and diversification of its Foundry’s capabilities, the future looks promising for Edelbrock, its partners and its clients.
The post Edelbrock Foundry: Expanding the Horizons of Aluminum Casting Education first appeared on Drag Illustrated | Drag Racing News, Opinion, Interviews, Photos, Videos and More.