3D Scanning to CAD: How Philadelphia Racing Products Overhauls the Product Design Process with Mesh2Surface for SOLIDWORKS®
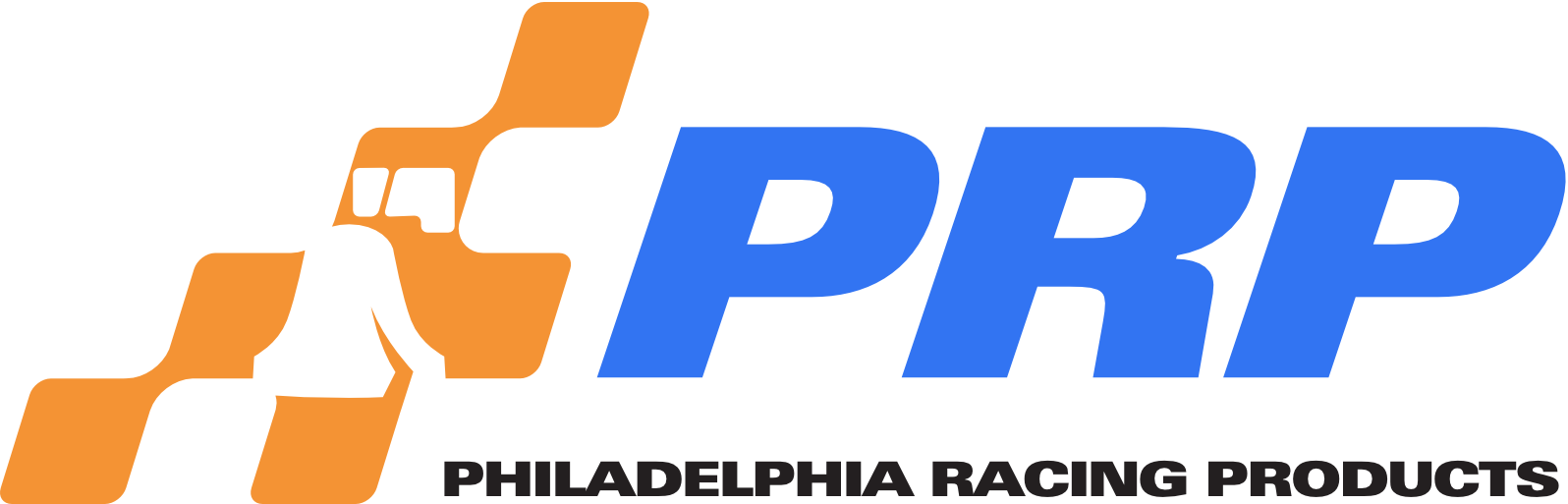
Philadelphia Racing Products (PRP) is a manufacturer of high-performance aftermarket automotive parts, dedicated to meeting the rigorous standards of racing enthusiasts. Established in 1991, PRP contributes much of its success to founder, Julius John Schonberger III, and his passion for street and performance racing. Recognizing an opportunity in the market, he shifted the company’s focus from selling ready-made parts to designing and manufacturing automotive components for sale. Three decades later, PRP has evolved to include a thriving performance engine division alongside its comprehensive racing parts manufacturing facility.
Today, Richard and Jay Schonberger, Julius’ sons, continue their father’s legacy and his love of racing. They are actively involved in all aspects of the operation—from managing day-to-day operations to designing, manufacturing, and track testing more than 1,000 automotive parts, motors, and engines. Additionally, the PRP team undertakes custom projects, ensuring the company remains at the forefront of innovation and excellence in the performance racing industry. All PRP products are proudly 100% American-made.
“Mesh2Surface for SOLIDWORKS® significantly improves our design and product development workflow, particularly in terms of accuracy and efficiency,” said Richard Schonberger, Co-owner and CEO of PRP. “Thanks to this Scan to CAD solution, we now have more time to focus on our core designs and create the best high-performance automotive racing products for our valued customers.”
Expanding the Business
Philadelphia Racing Products (PRP) has been in business for more than 30 years. Growing a company year over year, as well as producing all of its products in-house in the USA, is no small feat. PRP continues to expand its operations by designing and manufacturing more high-performance automotive racing parts, along with a thriving custom work division. In response to the increasing demand for custom projects, Richard Schonberger, co-owner and CEO of PRP, recognized the necessity for improving the efficiency of the company’s product design workflow.
Schonberger explained, “For our reverse engineering projects, our engineering team used to take part measurements by hand with tools such as calipers, micrometers, height gauges, and gauge blocks. Then, they verified the measurements by printing out paper templates. This method was both a time-consuming and tedious process. To keep up with the growing demands from our customers, we need to find a better solution.”
PRP’s product design work is split between reverse engineering existing parts and designing products from mating parts, such as a valve cover, where getting a precise fit is essential.
Some of the challenges PRP’s team faced with the conventional method include:
Difficulty in accurately measuring moderate to extremely complicated parts.
Accurately assessing clearances.
Ensuring proper fitment and mating of assemblies and other components.
“Nowadays, whenever the subject of reverse engineering or design is brought up, you’re more than likely to talk about 3D scanning as well,” said Schonberger. “Exploring the Scan to CAD approach for product design and development seemed like a promising route for our business to scale.”
Scan to CAD For Better and Faster Product Design
Scan to CAD involves using mesh data captured by a 3D scanner and importing it into reverse engineering software or a plugin to guide the creation of a professional CAD model.
The ‘Scan to CAD’ approach to product design starts with a high-quality 3D scanner swiftly capturing millions of surface measurements from a physical object. The resulting 3D mesh is then imported into a 3D reverse engineering software, or a design software like SOLIDWORKS® with the help of a dedicated Scan to CAD solution. This 3D mesh serves as a reference for extracting and creating primitives, planes, or cylinders for designing the new part. The result is a comprehensive 3D CAD model suitable for any production needs.
“Our engineering team consists of Chase Evans, our Lead Engineer, and Guy Porter, our Design Engineer, who are both experienced users of SOLIDWORKS®. We were looking for a reverse engineering software that would act as the bridge between our 3D scanner and our preferred CAD software,” said Schonberger.
After reaching out to 3D scanning technology supplier GoMeasure3D about their needs, the PRP team got a demonstration of Mesh2Surface for SOLIDWORKS®, developed by KVS. As Mesh2Surface’s authorized reseller in the United States, GoMeasure3D offered the PRP team insights into how this Scan to CAD solution could benefit its product design and development workflow. From that moment on, everything fell into place. Since then, the PRP team has been using Mesh2Surface for SOLIDWORKS® regularly for over a year.
“Mesh2Surface has been instrumental in helping our team overcome many challenges,” said Chase. “Previously, we had to first model the existing component before we could even create the mating part, which ultimately is the product we want to design and manufacture.”
With Mesh2Surface, the engineering team can directly design a mating part without the need for a roundabout approach, which results in huge time savings.
“Now, for instance, when we design a custom valve cover for a head, all we have to do is capture the surface measurements of the head with a 3D scanner to obtain measurements such as the bolt-hole locations, valve train geometry, and rail locations,” said Chase. By referencing the 3D mesh of the physical component, we can dedicate all our time to designing the custom valve cover and significantly simplify the process.”
Client Project Highlight
The PRP team used Mesh2Surface for SOLIDWORKS to design a custom engine valve cover for a Chevrolet ‘Big Block’ motor in a hydroplane racing boat.
Fit Like A GloveThe newly designed custom cover (CAD – at the top) is positioned on top of the cylinder head
(3D scan data – at the bottom).
The Completed ProjectRoger Mahan Motorsports LLC, a PRP customer, fitted one of its racing hydroplane boats with the engine cover designed by PRP.
“We’re also designing better products using this new approach because we can fully trust the reference measurements captured by our 3D scanner for designing our parts, compared to the hand tools we used previously,” Schonberger explained. “Using the 3D mesh data to determine clearances and ensure the proper fit of mating parts becomes significantly easier and faster. As an extra advantage, the parts our team is designing are extremely accurate.”
Billet LS Timing CoverThe Billet LS Timing Cover is an aluminum casing that mounts to the front of a LS engine. It creates a protective housing for the engine’s timing components, preventing dust, dirt, and other particles from interfering with the engine’s performance. Mesh2Surface for SOLIDWORKS® was essential for finding the exact hole locations to mount the cover, as well as for precisely measuring the position of the crankshaft flange.
“By using the Scan to CAD approach to product design, we see significant efficiency gains in our product design workflow,” said Chase Evans, PRP Lead Enginner. Drawing from my own experience, on average, the time required to design a part is now reduced down to approximately 25% of the original time or less.”
Plugin Versus Standalone Software
The PRP team found that the combination of SOLIDWORKS® native tools with the Mesh2Surface Scan to CAD toolsets produces exceptional synergy. “Some designers and engineers prefer standalone reverse engineering software. However, as an experienced SOLIDWORKS® user, I found it more practical to perform reverse engineering all within one CAD software package,” said Chase.
“Mesh2Surface as a plugin works perfectly well with SOLIDWORKS® by allowing me to access a comprehensive set of advanced reverse engineering tools. With this seamless integration, I can fully harness the potential of both platforms, significantly enhancing my product design and development workflow in multiple ways.”
Scan to CAD Makes the Verification Process Much Easier
Another advantage of using Mesh2Surface is that it makes the verification process significantly easier. This process ensures the proper fit and functionality of the designed part. By using precise 3D scanned data in combination with the Mesh2Surface tools for the reverse engineering process, the PRP team can now accomplish 90% of the verification process digitally, right there in the model instead of constantly having to go back and check the mating parts. The PRP team is now more confident going into the physical prototyping stage that all fitment and clearances have been accurately accounted for.
Billet LS FlexplateThe Billet LS Flexplate connects the engine’s crankshaft to the transmission’s torque converter. It is then fitted with a gear to connect to the starter, which simultaneously starts both the engine and the transmission when you turn the key. Mesh2Surface for SOLIDWORKS® played an important role in determining the proper clearance and spacing when designing the LS Flexplate. The product incorporates a built-in spacer that could only have been designed using this Scan to CAD plugin solution.
Customer Responsiveness
Chase conveyed his highest compliments for the responsiveness of the Mesh2Surface developers. He said they highly value user feedback, taking the end user’s considerations seriously.
“The ability to interface closely with the product development team at Mesh2Surface is great. I once gave my feedback on a new feature I thought would be useful. The following week I downloaded an updated version of the software and it was right there!”
Drawing from his experience with other software companies, Chase emphasized that he doesn’t encounter the same level of customer attentiveness as he does with KVS. He is very happy that Mesh2Surface developers use his suggestions to improve the software.
The PRP Team’s Favorite Mesh2Surface for SOLIDWORKS® Features
“Heading the design of new products, I believe that simplicity, precision, and innovation are at the core of design and development,” said Guy Porter PRP Design Engineer. “Mesh2Surface’s utility provides sustainable accuracy in our designs and has a dramatic impact on the efficiency of our workflow.”
These Mesh2Surface for SOLIDWORKS® features significantly enhance PRP’s reverse engineering projects:
The fitting algorithms are remarkably accurate.
Ability to easily extract primitives, planes, or cylinders.
Decimating 3D mesh data with a large file size makes reverse engineering much more manageable and efficient.
Visualization of the percentage of the points that are within the tolerance from the reference mesh within the Deviation Analyzer tool.
Ability to align mesh by reference.
The ease of taking multiple cross sections, and the ability to utilize the ‘Fit Sketch Entities’ tool to extract SOLIDWORKS® sketch entities to the cross sections.
Ability to pull 3D meshes into an assembly and reverse engineer them.
The PRP team finds Mesh2Surface for SOLIDWORKS® to be of great value.
“We get a lot of functionality for the price. Our team particularly appreciates the simplicity of Mesh2Surface–it gets the job done without the complexity,” said Chase. The learning curve is great and it’s easy to use. It’s a very impressive reverse engineering solution that fits our company’s needs.”
Big Block Chevy (BBC) Stud GirdlesBig Block Chevy Stud Girdles are a set of bars that bolt together to clamp onto a valve train’s poly locks. This part helps increase the rigidity of the valve train and provides more support in cases of an aggressive camshaft. Mesh2Surface for SOLIDWORKS® was instrumental in finding the precise angles of the poly locks. Each piece sat at a compound angle, which would be practically impossible to accurately design without this Scan to CAD plugin.
It’s fantastic that we achieved our goals by using Mesh2Surface for SOLIDWORKS®,” Schonberger remarked. “We’ve successfully transformed our product design process through 3D digitization, allowing us to streamline our workflow instead of relying on conventional manual methods as we did before. We’re excited to further expand our operations with this overhaul of our reverse engineering design workflow. Now, we can handle more projects, serve new clients, and tackle extremely complex design tasks.”
For individuals seeking a standalone Scan to CAD solution, KVS also developed QUICKSURFACE which performs similarly to Mesh2Surface. Mesh2Surface plugin is currently available for SOLIDWORKS® and Rhino CAD software packages.
* SOLIDWORKS® is a trademark of Dassault Systèmes. Rhinoceros is a registered trademark of Robert McNeel & Associates. Mesh2Surface is an independent product developed by KVS Ltd.
This story was originally published on November 21, 2024.
The post 3D Scanning to CAD: How Philadelphia Racing Products Overhauls the Product Design Process with Mesh2Surface for SOLIDWORKS® first appeared on Drag Illustrated.